How Is Vacuum Coating Used for PVD Stainless Steel
PVD Stainless Steel Vacuum Coating Process
Step 1: Substrate Preparation
For the vacuum coating to adhere properly to stainless steel, substrate prep is the critical first step. Any oil, dust, or even fingerprints left on the surface can compromise the coating’s performance. Therefore, cleaning is a must.
- Cleaning the Stainless Steel Surface: Ultrasonic cleaning machine is recommended. Throw the stainless steel parts in, add a mild cleaning agent, ultrasonic vibration for a few minutes, you can shake the oil and dust. It takes a lot less work than scrubbing by hand, and it’s completely clean.
- Surface Treatment Tips: After cleaning, the surface might still not be smooth enough. You can lightly sand it with sandpaper or use a polishing machine. Controlling roughness helps the coating grip better. Typically, sanding with 400-600 grit sandpaper does the trick, but it depends on your equipment and needs.
Step 2: Vacuum Chamber Setup
Next up, the vacuum environment is the heart of PVD technology. You need a nearly air-free space to make it work, so setting up the vacuum chamber in your coating machine is key.
- Vacuum Level Control: Aim to pump the vacuum down to 10⁻⁵ Torr or lower. This ensures air molecules won’t mess with the coating material as it deposits. Too much pressure can lead to uneven layers or even tiny bubbles. A solid vacuum pump can hit this level in minutes.
- Common Equipment: Magnetron sputtering systems are a go-to for PVD. When installing the target (like titanium or chromium), make sure it’s secure. Adjust the power supply’s current and voltage based on the target size—check the manufacturer’s manual for suggested values. Don’t skip checking the cooling system either, or the machine might overheat during long runs.
Step 3: Coating Material Selection
Picking the right coating material can make your PVD-coated stainless steel both functional and stylish. Different materials bring different perks, so choose based on what you’re using it for.
- Titanium Coating: Corrosion resistance is its superpower. If you’re working on kitchenware or outdoor gear, a titanium coating can keep rust at bay for years while adding a subtle golden shimmer.
- Chromium Coating: High hardness and wear resistance make it perfect for tool surfaces like knives or molds. Plus, chromium gives a bright, modern finish that looks sharp.
- Matching Your Needs: Want some color on your stainless steel? Add nitrogen for gold or black tones, or oxygen for blues and rainbow effects. The exact mix takes some trial and error, but higher nitrogen levels usually pump up the gold vibe.
Step 4: Deposition Process
With materials and setup locked in, deposition is the main event. This step nails down the coating’s thickness and quality.
- Parameter Tips: Keep the temp between 150-500°C. Too hot, and the steel might warp; too cool, and it slows down. Aim for 30-60 minutes, tweaking based on thickness. Thin layers are quick; thicker ones take more time.
- Ensuring Evenness: Uneven coating looks awful. Rotate the substrate in the chamber or adjust the target angle so metal particles hit evenly. Most sputtering rigs have this feature, just dial it in.
Step 5: Post-Processing
After coating, post-processing locks in stability and prevents cracks or peeling down the line.
- Cooling Tricks: Don’t yank the parts out right away. Let them cool slowly in the chamber after shutting off the heat. Fast cooling can cause cracks from uneven shrinking. Room temp usually takes 1-2 hours, so chill out.
- Quality Check: Test the coating’s worth. Use a hardness tester or lightly scratch it to see if it holds. Worst case, eyeball it for bubbles or color flaws to get a rough idea.
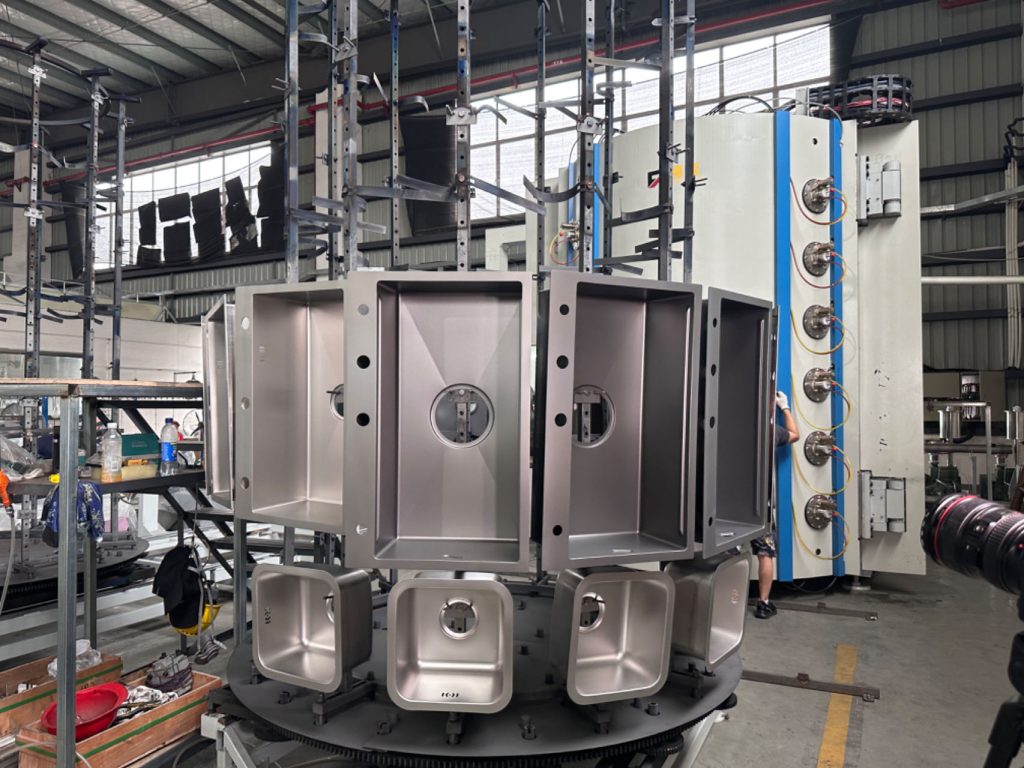
Vacuum Coating Brings Vibrant Colors
Coating Color-Tuning Process
Vacuum coating works by turning metal materials into gas inside a machine and sticking them onto stainless steel. Want gold or rose gold? It’s all about the materials and gases you use. For example:
- Titanium and Nitrogen Mix: Heat up titanium until it evaporates, add a bit of nitrogen, and you’ve got that classic gold look on stainless steel. You’ll see this on faucets or door handles a lot, giving a high-end, timeless vibe.
- Tweaking Gas Ratios: Bump up the nitrogen, swap in oxygen, or toss in a pinch of carbon, and the color shifts from gold to rose gold or even a pinkish hue.
This isn’t guesswork. Techs dial in the pressure (around 0.5 Pa) and temp just right to keep the color even and locked in. Big U.S. home brands swear by this trick, coating stainless steel parts so every edge matches perfectly.
If you’re sprucing up your place or picking furniture, this tech lets you customize stainless steel pieces easily. Think gold bathroom faucets or rose gold cutlery in the kitchen. The color’s yours to choose, and it sticks around for the long haul.
Triple Protection from the Coating
Vacuum coating doesn’t just slap a new shade on PVD stainless steel. That layer it adds brings real perks, blending style with function. Here’s how it pulls it off:
- Scratch and Wear Resistance: This isn’t some flimsy paint job. It’s tough stuff like titanium. Picture a gold faucet you twist daily and rinse constantly. Years later, it’s still shiny. U.S. tests show this coating can handle tens of thousands of rubs, way outlasting spray paint.
- Corrosion Boost: Stainless steel already fights rust decently, but the coating takes it up a notch. Materials like titanium block moisture and salt, perfect for coastal spots or steamy kitchens.
- Rock-Solid Grip: Applied in a vacuum, the coating bonds tight to the steel, unlike paint that flakes off. Take a hotel using PVD stainless door handles: five years in, the color and shine barely budge, cutting maintenance costs big time.
If you’re after stainless steel that looks good and lasts, vacuum coating’s a solid pick. Whether it’s a colored sink at home or jazzed-up dinnerware, this layer keeps things durable and low-effort to maintain.
Improving PVD Steel Wear Resistance
How Coating Materials Strengthen the Surface
Vacuum coating ramps up stainless steel’s toughness by adding a rock-hard layer to its surface.
- How It Works: In a special coating machine, technicians will use the PVD method to turn metal materials such as titanium and chromium into tiny particles, and then firmly “stick” to the stainless steel surface. The coating is just a few micrometers thin, but surprisingly hard. For example, after plated with titanium nitride (TiN), the hardness of stainless steel can jump from the ordinary 200-300 Vickers hardness (HV) to more than 2000 HV, which is several times stronger than when not coated.
- Why It Matters: Picture a stainless steel kitchen sink: uncoated, it’ll scratch up within months of daily abuse from pots and pans. But with vacuum coating, the surface becomes armor-plated, shrugging off impacts without a mark. Tests show this can boost hardness 5-10 times, perfect for heavy-duty spots like cutlery, tools, or door handles. If you want stainless steel that can take a beating, this does the trick.
How the Tech Fights Daily Wear
Beyond jacking up hardness, vacuum coating helps PVD stainless steel hold up against everyday wear and tear.
- What’s the Secret?: PVD doesn’t just slap on a hard layer; it fuses it to the steel like glue. The machine vacuums out air, then blasts the material onto the surface with heat or electric fields, creating a smooth, dense shield. This layer’s not only tough but slick, with low friction, so stuff slides off instead of digging in.
- Real Results: Think about stainless steel forks and knives. Regular ones get scratched up over time, but PVD-coated ones stay smooth even after years of washing and clanking. In tests, uncoated steel scratched after 500 rubs on a wear machine, while coated steel took 5000 rubs to show a hint of damage. That scratch resistance is a game-changer for busy kitchens or frequently used furniture hardware. It’s a solid pick for durability with less hassle.
Why Choose Vacuum Coating
Vacuum coating beefs up PVD stainless steel’s wear resistance with a one-two punch of hardness and scratch protection. The materials bring the strength, and the process seals the deal. Whether you want a scratch-free sink or longer-lasting knives, this tech delivers. It’s not just talk; countless tests back it up. Pick the right coating material and a decent machine, and your stainless steel gets tougher, more wear-resistant, and way easier to live with.
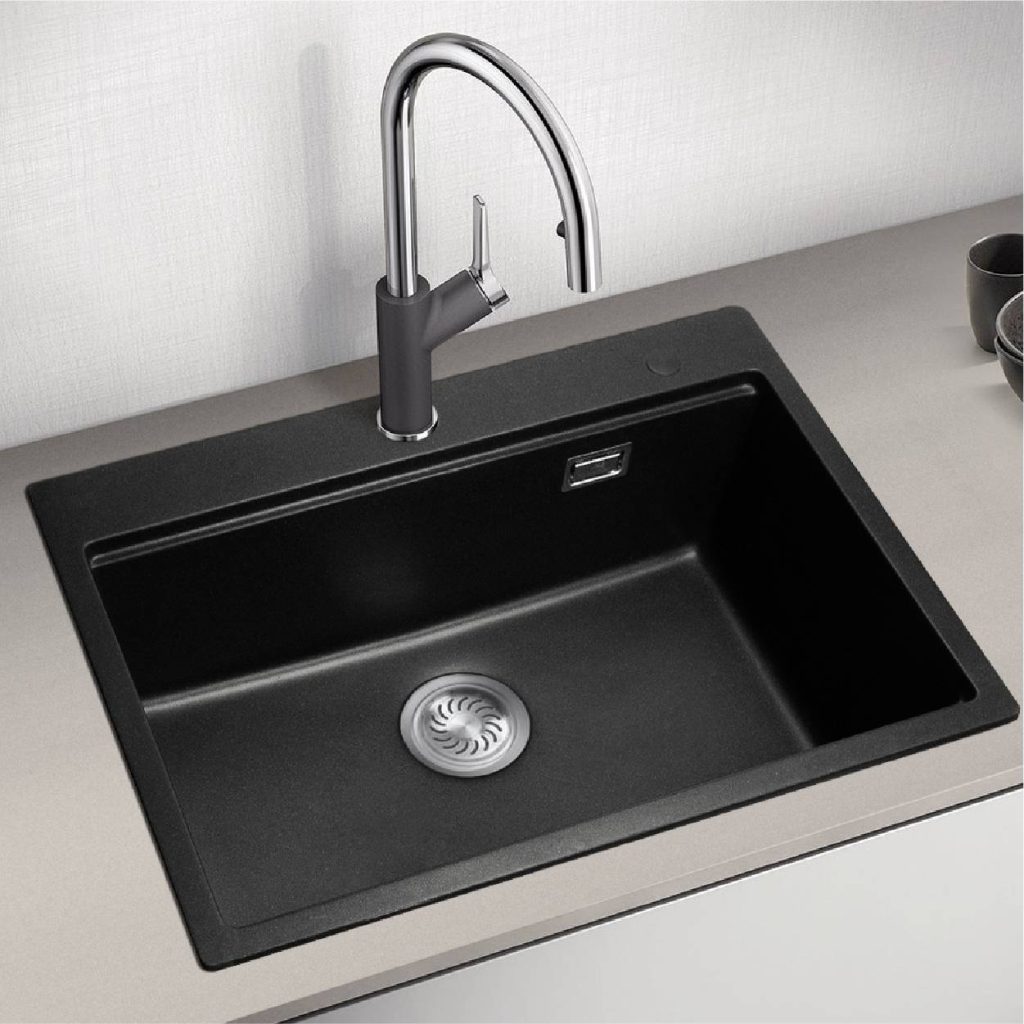
PVD-Coated Stainless Steel in Action
The term “vacuum coating” might sound fancy, but it’s already snuck into our daily lives and all sorts of industries, especially with stainless steel treated using PVD (Physical Vapor Deposition) tech.
Decorative Coating
Vacuum coating gives stainless steel a stunning makeover, and you can spot it all over the house.
- In the bathroom, those faucets gleaming with gold or rose gold? That’s PVD coating at work – a high-tech finish applied to stainless steel that resists scratches and never fades. It stays brilliant for years, perfect for style lovers who hate maintenance.
- In the dining room, those stainless steel forks and knives with a black-gold or copper vibe? Vacuum coating’s the trick. The color is reliable, and the dishwasher is not afraid of wear and tear when thrown into it, which is practical and classy.
Industrial Coating
In factories, vacuum coating makes stainless steel tough enough for the heavy stuff.
- Machine parts, like cutting tools in a workshop, often use PVD stainless steel. The coating’s hard and slick, cutting down wear and sticking, so tools last longer and work better. Tons of manufacturers lean on this to save cash.
- Stainless steel pipes, especially those used in chemical plants, become highly resistant to acid and alkali corrosion when coated with protective films. These pipes offer a safe, durable solution for industrial applications, significantly reducing the need for frequent replacements.
Automotive Uses
Cars have vacuum coating in the mix too, making stainless steel parts perform like champs.
- Inside the engine, stainless steel bits like piston rings get a hard coating that cuts friction and handles heat. You can drive cross-country without worrying about breakdowns, and carmakers use this to stretch part life by thousands of miles.
- Outside, those stainless steel trim pieces, like door frames, get a rust-proof, glossy layer. They hold up through rain and sun while looking sharp, ideal for car lovers who want style and strength.
Sanitary Coating
Vacuum coating even steps up stainless steel’s game for cleanliness.
- In food processing plants, stainless steel countertops or tools with an antibacterial coating keep germs at bay. After a long day, cleanup’s a breeze, making it a go-to for spots that need to stay spotless.
- In hospitals, surgical tools made of stainless steel get a layer with antibacterial properties, lowering contamination risks. It’s a solid choice for gear that needs to be safe and reliable.
Vacuum Coating Perks and FAQs
Perks
- Greener Than Electroplating: No Waste Liquid Traditional electroplating churns out messy waste liquid that’s a pain to deal with and bad for the planet. Vacuum coating flips the script. It gets the job done in a sealed vacuum using gases and physical reactions to layer the coating onto stainless steel, leaving zero wastewater behind. For places with tough eco rules, like some strict U.S. states, it’s a game-changer. Going this route makes your products greener and cuts costs on waste cleanup.
- Tougher Coatings: Hardness Tops HV2000 Coatings made with PVD and vacuum coating are insanely hard, easily hitting over HV2000. What’s that mean? Picture your stainless steel sink or knives with a surface that laughs off scratches and wear, staying shiny for years. Compared to standard coatings, this durability makes it perfect for products that need to stand up to constant grinding.
Common Issues and Fixes
Sure, vacuum coating isn’t perfect, and you’ll hit some snags along the way. But don’t sweat it, there’s a fix for every hiccup.
Issue 1: Coating Peeling
- Why It Happens: Usually, the stainless steel wasn’t cleaned right. Oil or dust on the surface means the coating won’t stick.
- Fix: Don’t cut corners on cleaning. Hit it with an ultrasonic cleaner and wipe it down with some alcohol to get it spotless. Spend an extra 10-15 minutes here, and you’ll see a night-and-day difference.
Issue 2: Uneven Color
- Why It Happens: Airflow in the vacuum chamber gets wonky, or the coating machine’s settings are off, so the layer’s thick in some spots and thin in others, leaving you with a patchy rainbow.
- Fix: Check the vacuum pump first to make sure it’s pulling air like it should. Then tweak the gas flow, like your nitrogen or argon mix, until it steadies out.
Issue 3: High Costs
- Why It Happens: For small projects, the gear and labor for vacuum coating can add up fast, making it feel like a bad deal.
- Fix: For small batches, rent the equipment instead of buying. Plenty of companies offer short-term leases. If you’re running big jobs, go all-in on an automated coating machine. Higher efficiency drops the per-piece cost right down.