How Target Materials Shape PVD Coating Hues
PVD coating can make products shine from golden to sleek black, looking good and tough. The target material is the key to controlling color, mixed with reactive gases, process settings, substrate prep, and where it’s used, all shaping the final look.
1. Target material sets coating color
The PVD coating process uses a target material reacting with gases in a vacuum to form compounds with specific colors. Here’s a table with common combos, clear and useful:
Target | Gas | Coating | Color | Typical Use |
---|---|---|---|---|
Titanium | Nitrogen (N₂) | titanium nitride coating | Gold | Wedding rings, decorative pieces |
Titanium | Acetylene (C₂H₂) | Titanium carbide (TiC) | Deep black | Drill bits |
Titanium | Oxygen (O₂) | Titanium dioxide (TiO₂) | Blue | Optical lenses |
Titanium | Nitrogen + Acetylene | Titanium carbonitride (TiCN) | Rose gold | Fashion bracelets |
Zirconium | Oxygen (O₂) | Zirconium dioxide (ZrO₂) | White | Medical implants |
Zirconium | Nitrogen (N₂) | Zirconium nitride (ZrN) | Light gold | Furniture handles |
Zirconium | Acetylene (C₂H₂) | Zirconium carbide (ZrC) | Dark gray | Industrial gears |
Chromium | Nitrogen (N₂) | Chromium nitride (CrN) | Silver-gray | Car rims |
Chromium | Acetylene (C₂H₂) | Chromium carbide (CrC) | Deep gray | Molds |
Aluminum | Oxygen (O₂) | Aluminum oxide (Al₂O₃) | Clear | Laser lenses |
Aluminum | Nitrogen (N₂) | Aluminum nitride (AlN) | Silver-white | Chip substrates |
Titanium Targets: The Versatile Star
Titanium targets are like the Swiss Army knife of the PVD coating process. They can churn out gold-colored TiN, black TiC, blue TiO₂, or rose-gold TiCN. They cover everything from wedding rings to aerospace turbine blades with PVD coating for cutting tools. The process is stable, colors stay consistent, and it’s great for big-batch production using sputtering deposition.
Zirconium, Chromium, Aluminum: Unique Strengths
- Zirconium Targets: White ZrO₂ works for medical devices. Light gold ZrN is perfect for fancy jewelry with PVD. Dark gray ZrC is tough and wear-resistant, good for industrial parts needing PVD coating durability.
- Chromium Targets: Silver-gray CrN fights corrosion, ideal for car parts with PVD metal coating. Deep gray CrC is super hard, great for molds using PVD coating for cutting tools.
- Aluminum Targets: Transparent Al₂O₃ or silver-white AlN is made for optics and electronics with PVD thin film coatings. They’re strong for protection.
Practical Tips for Picking Targets
Choose targets based on the job. Titanium targets are good for colorful or wear-resistant needs. Zirconium targets shine for light-colored decoration with PVD finishing process. Chromium targets are best for functional coatings. Aluminum targets focus on optics. Go for 99.99% pure targets and pair them with high-precision PVD vacuum coating machine gear. Stick with suppliers who have ISO 9001 certification for PVD coating suppliers to save headaches. Check the target’s uniformity and batch consistency to avoid color issues.
2. Gas Control for Color Depth
Gas ratios and flow rates are the color palette for PVD coating. Small tweaks can shift the hue and depth. Using a titanium target as an example:
- Nitrogen gas: More nitrogen makes TiN gold color pop, perfect for fancy watch cases. Less nitrogen gives a softer, subtle look.
- Acetylene gas: Bump up acetylene for a blacker TiC, tough and wear-resistant, great for screwdrivers.
- Oxygen gas: Creates blue TiO₂ or white ZrO₂, but too much oxygen can turn it whitish, messing up the look.
Flow Rate Tips
- Gold TiN: Keep nitrogen flow at 20-50 sccm for that classic gold shine. Below 20 sccm, it’s too pale. Above 50 sccm, it leans reddish.
- Black TiC: Acetylene flow at 10-30 sccm. Higher flow means deeper, harder black. Ramp up acetylene slowly for even results.
- Blue TiO₂: Oxygen flow at 5-10 sccm, under 10% of the mix, to avoid color patches.
Things to Watch
- Stick to 20-50 sccm nitrogen for stable gold, 10-30 sccm acetylene for tuning deep black, and keep oxygen below 10%.
- Use high-precision flow meters and vacuum coating equipment to track gases and cut down on trial-and-error costs. Calibrate flow controllers regularly to keep colors consistent across batches.
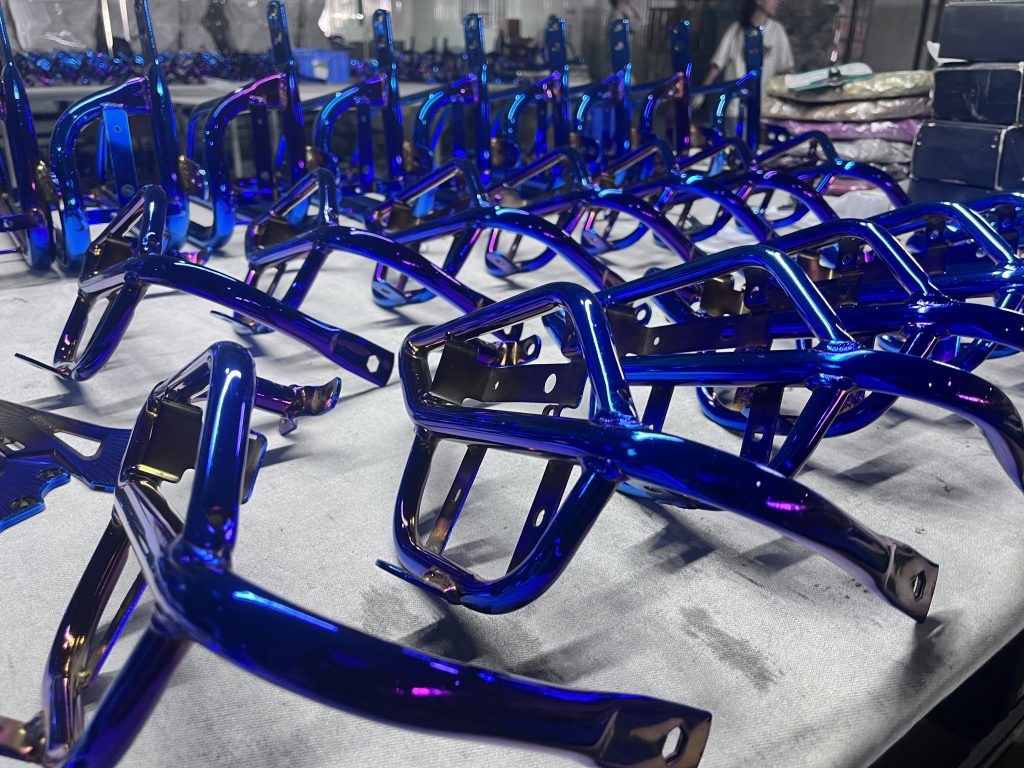
3. Process Parameters for Consistent Results
Process parameters are critical for keeping PVD coating colors consistent. Sputtering power, vacuum level, and substrate temperature directly affect the outcome.
Sputtering Power Basics
Sputtering power, ranging from 2 to 5 kW, controls the color depth:
- High power (4-5 kW): Best for dark coatings like TiC. It gives a fast deposition rate and rich color, often used for durable cutting tools.
- Low power (2-3 kW): Works for lighter coatings like TiN or ZrO₂. The color is softer, perfect for stylish jewelry.
Vacuum & Temperature Control
- Vacuum level: Keep it at 10⁻³ Pa to ensure pure reactive gases. Impurities can make TiN look yellowish or TiO₂ turn whitish in the PVD coating process. Calibrate the vacuum pump weekly using reliable vacuum technology.
- Substrate temperature: Stay below 200°C to avoid coating cracks or color shifts, like ZrN turning darker in the PVD finishing process. Low-temperature deposition suits decorative coatings for better durability.
Optimization Tips
- Use 4-5 kW for dark coatings and 2-3 kW for lighter ones, with real-time power monitoring.
- Maintain a 10⁻³ Pa vacuum level and check the vacuum chamber for leaks.
- Keep substrate temperature under 200°C, ideal for high-end jewelry.
Recommendations
Adjust power flexibly, stabilize the vacuum level, and control temperature. Invest in power monitoring tools and high-quality PVD vacuum coating machines to ensure batch-to-batch color consistency. Choose suppliers with solid maintenance records for more reliable equipment stability.
4. Substrate Surface Affects Color & Shine
The way you treat a substrate surface determines the shine and feel of a PVD coating. Polished or brushed finishes each have their own vibe, directly affecting how the color comes out.
Polished vs. Brushed
- Polished Substrate: A mirror-like finish makes gold TiN pop, perfect for wedding bands or jewelry. Polish it to a roughness of Ra under 0.1μm, and the color looks vivid, like a bright gold PVD coating.
- Brushed Substrate: A matte texture gives black TiC a tough, understated look, great for screwdrivers or cutting tools. Keep the texture direction consistent to avoid color patches in PVD finishing.
Polishing Tips
- Polish to Ra below 0.1μm and use ultrasonic cleaning to remove grease for a glossy TiN or ZrN finish on stainless steel. This works well for watch cases or necklaces, giving a high-end feel to jewelry.
- Clean thoroughly to make sure the coating sticks right.
Brushing Basics
- Keep the texture direction uniform and check for scratches. CrC or TiC coatings look best for cutting tools. This style suits industrial parts since the texture hides minor wear, boosting durability.
- A brushed finish stays good-looking and tough.
Recommendations
Go with a polished substrate for wedding rings and a brushed one for industrial parts. After polishing, clean the surface completely. For brushing, ensure the texture stays consistent. Pair with top-notch vacuum coating machinery, and the color and texture will level up. Always inspect the substrate for defects to guarantee the coating adheres well.
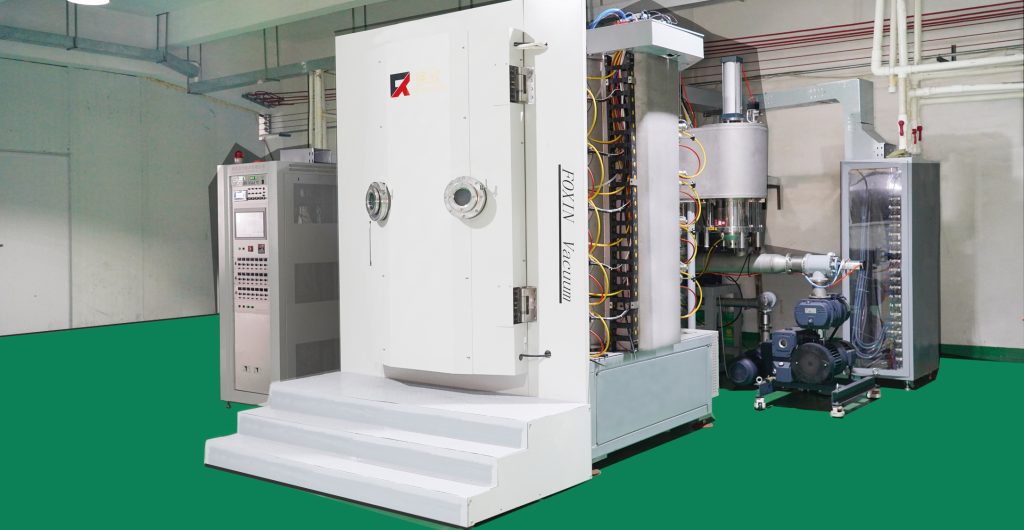
5. Guide for Choosing Applications
PVD coating varies by application. The table below sums up coating traits and uses, clear and straightforward:
Coating | Color | Traits | Applications |
---|---|---|---|
TiN | Gold | High hardness, wear-resistant | Wedding rings, aerospace blades |
TiCN | Rose gold | Smooth, scratch-resistant | Bracelets |
DLC | Black | Ultra-hard, stylish | Sports watches |
ZrN | Light gold | Corrosion-resistant | Offshore drilling gear |
Jewelry and Watches
- TiCN: Gives a rose gold vibe, perfect for bracelets and earrings. Polished surfaces make the rose gold PVD coating pop with shine.
- DLC: Black and tough, great for sports watches or high-end earbuds. Scratch-resistant, it handles daily bumps without a mark.
- TiN: Gold and fancy, ideal for dress watch cases with gold PVD coating.
Industrial and Special Uses
- TiN: Super hard, works for aerospace turbine blades or cutting tools. The gold look of the PVD coating adds a premium feel.
- ZrN: Corrosion-resistant, good for ocean drilling gear or coastal pipelines. Shines in salt spray tests for PVD coating durability.
- DLC: Ultra-hard, fits medical surgical tools, tough and biocompatible as a PVD coating material.
Practical Tips
- TiN handles high-wear situations, TiCN is more for decoration, DLC is stylish and durable, and ZrN fights corrosion.
- Use high-precision PVD vacuum coating machines and quality targets from PVD coating suppliers to nail coating performance. Test coating hardness and adhesion to match the job.
6. Eco-Friendly Processes Boost Value
Environmental Benefits of PVD
The PVD coating process skips cyanide and heavy metals, recycles waste, and cuts emissions by 50% compared to electroplating. Gold TiN or black PVD coating meets ISO 14001 standards, making it ideal for wedding rings, medical devices, and other high-demand uses with green coating technology. One watch brand leaned into PVD to boost its green image and saw a 15% jump in market share.
Recycling Target Materials
Titanium and zirconium targets can be recycled and reused, slashing production costs by 30% for PVD coating cost. For example, after making TiN or ZrN coatings, leftover target material can be remelted, perfect for mass-producing cutting tools or PVD coated furniture parts.
Optimizing Waste Gas Recovery
High-efficiency gas recovery systems keep nitrogen and acetylene emissions low. Modern coating equipment with filtration cuts waste gas by 80%, aligning with green manufacturing trends. This reduces environmental impact and strengthens brand appeal in markets like jewelry and automotive parts with PVD metal plating.
Value-Adding Steps
- Highlight PVD’s non-toxic, recyclable nature to attract eco-conscious customers, especially in the high-end PVD coating jewelry market.
- Invest in gas and target recycling systems to cut waste and lower long-term PVD coating cost india.
- Pick suppliers with green certifications to ensure targets and PVD vacuum coating machines meet eco-standards.
Conclusion
By precisely matching targets, gases, settings, and substrates, PVD coating delivers everything from dazzling gold to sleek black finishes. Invest in top-notch coating machinery and green tech, and choose Foxin as your go-to PVD coating suppliers to create stunning, durable products that win over the market.